http://www.speedhunters.com/2016/03/project-kp61-finicky-bits-begin/FINAL CHAPTERA Surge Of Motivation
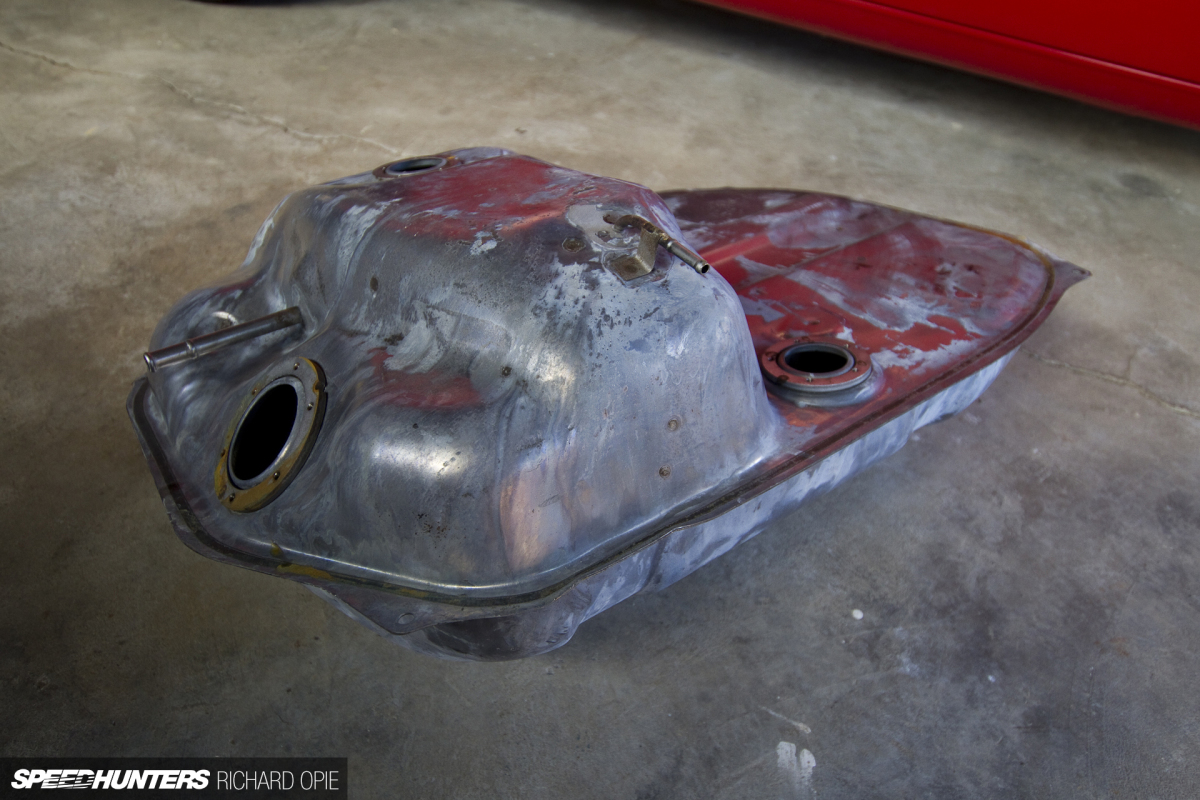
Mounting the engine, the gearbox, and even shortening the diff to suit the car – all of that could be considered the ‘fun’ bits of piecing together a project build. The not so fun bits? Putting the ‘services’ throughout the car. Likened to a building, this is the plumbing, the wiring, the fuel system – and this, possibly the single most boring photo ever posted on Speedhunters of the car’s original fuel tank post-acid dipping exemplifies the initial enthusiasm with which I approached the task of fuel.
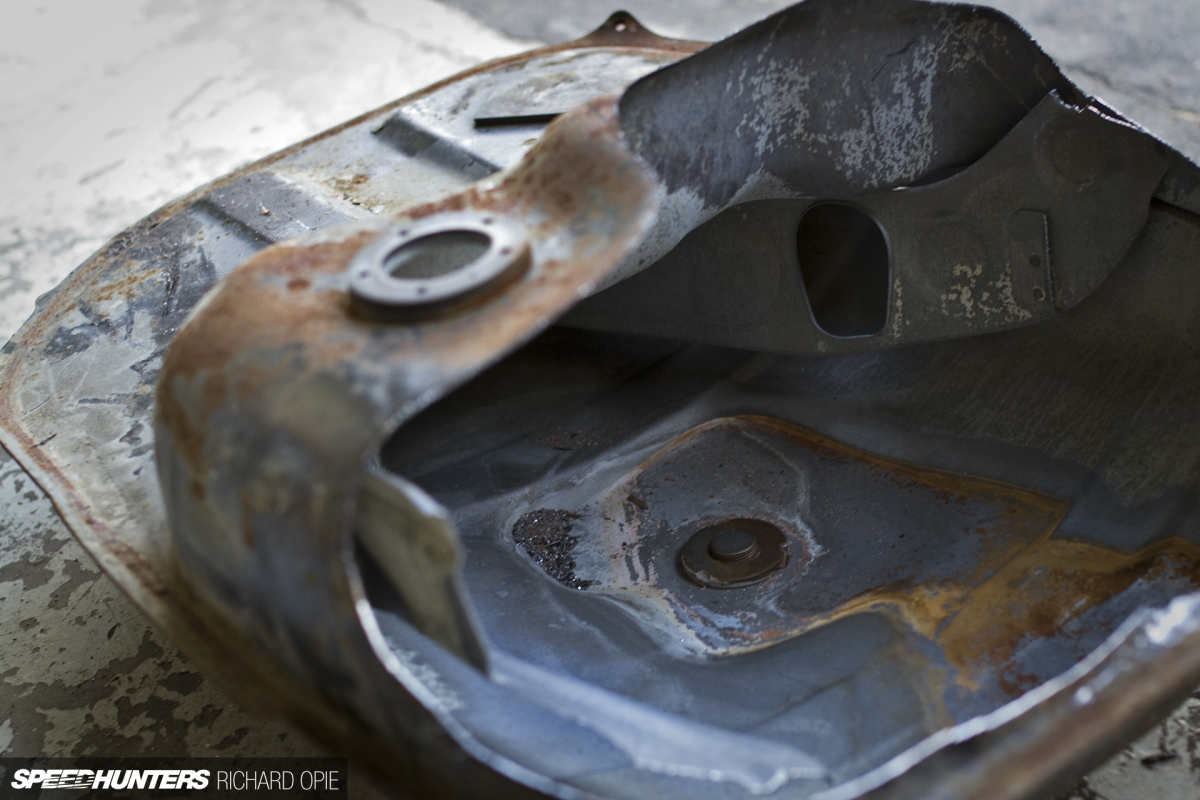
In a nutshell, the original tank, designed to suit a carburettor, wasn’t going to suit the fuel system in its standard state. That is to say, I wanted an in-tank type pump with no mucking around with lift pumps, surge tanks and main pumps all cluttering the underside of the car. So we needed to design and build a means of preventing fuel surge and accommodating an in-tank EFI-type fuel pump. This job was entrusted to Jon and Chris of Strange Workshop in Auckland, who also did some top-notch work on Taryn and Pedey’s
Project Z a while back. The first step was to chop open a sacrificial tank, and work out what we were dealing with.
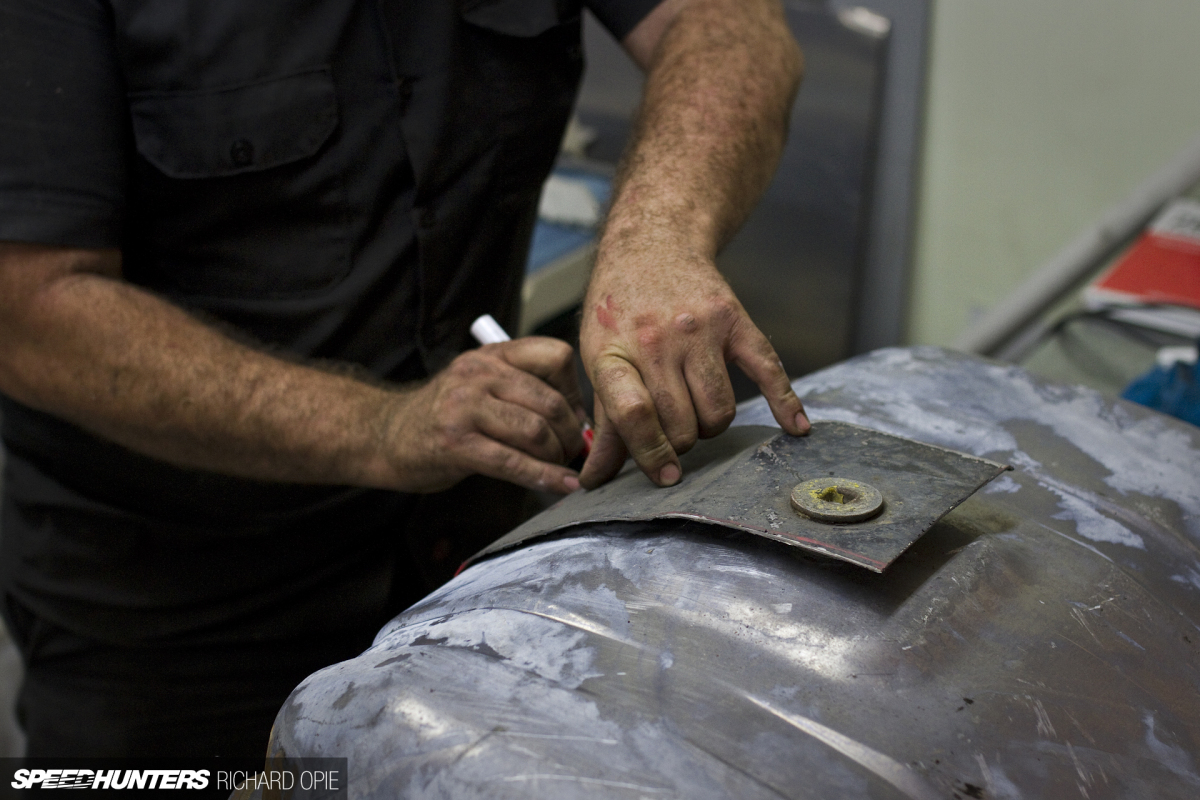
Once the location for the inbuilt surge compartment was ascertained, why not make it easy by cutting the required section out of the scrap fuel tank, transcribing the measurements onto the ‘good’ tank and marking it out ready for cutting.
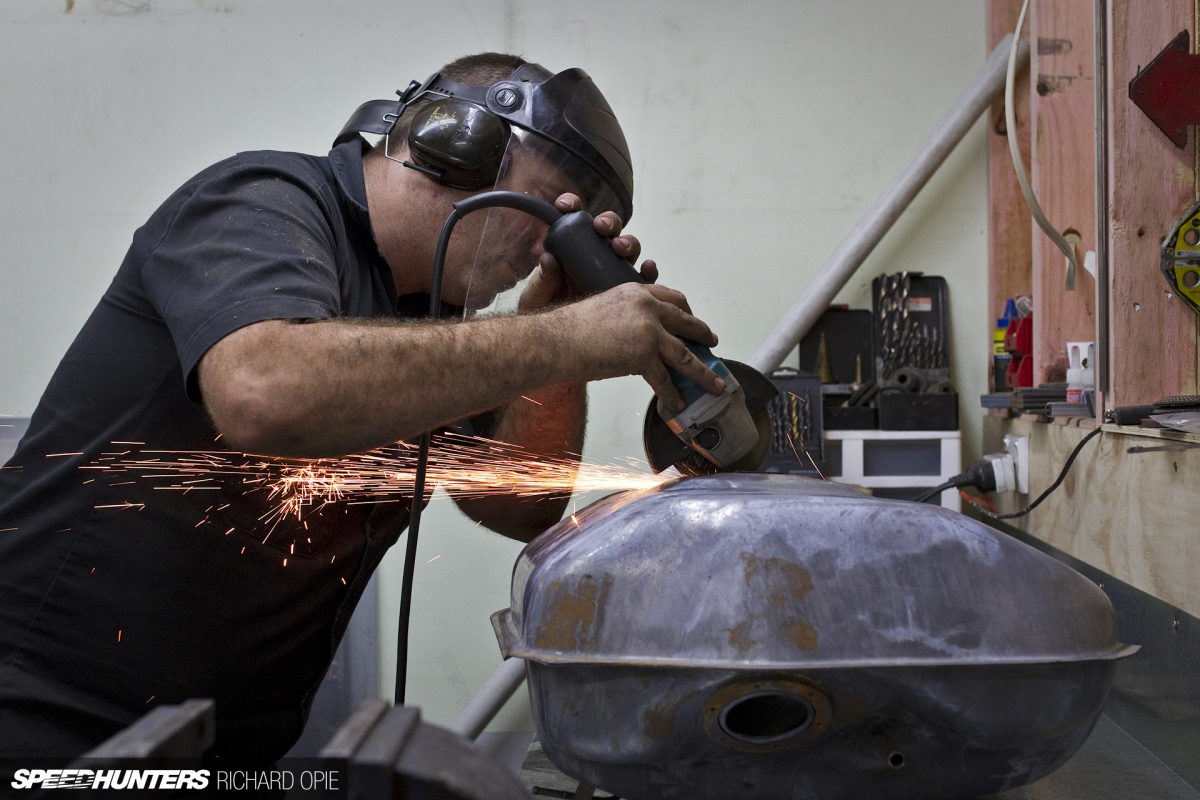
Jon’s a deft hand with a grinder, taking on an ‘easy does it’ mantra. The old adage of measure twice, cut once, was adhered to as the grinder made short work of the factory steel tank.
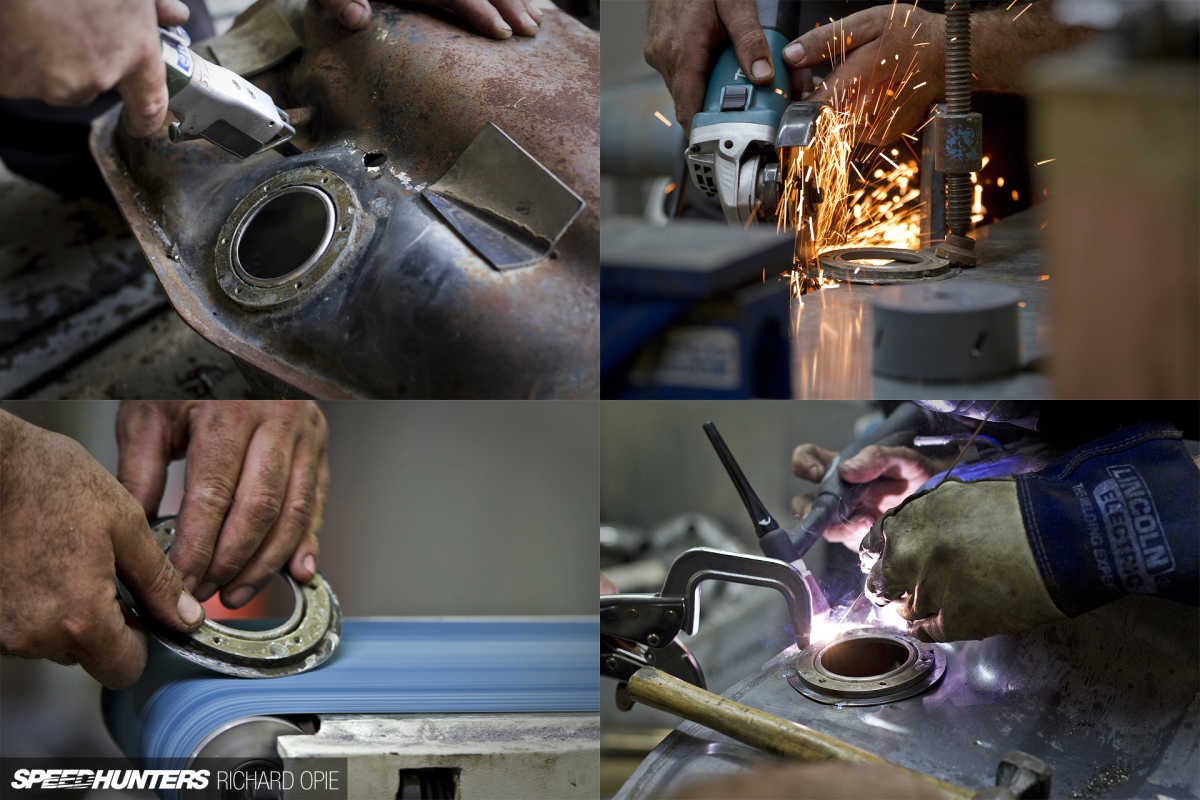
The scrap fuel tank also donated the flange which would accept the new fuel pump cradle; incidentally this flange originally served as the filler for the tank. The flange was chopped out, ground and linished to a round shape then welded in place on the tank where the original carb fuel lines would have been located.

In the meantime, Chris cracked on with the surge tank, folding up a compartment of roughly 3-litres in capacity using some fresh sheet metal.
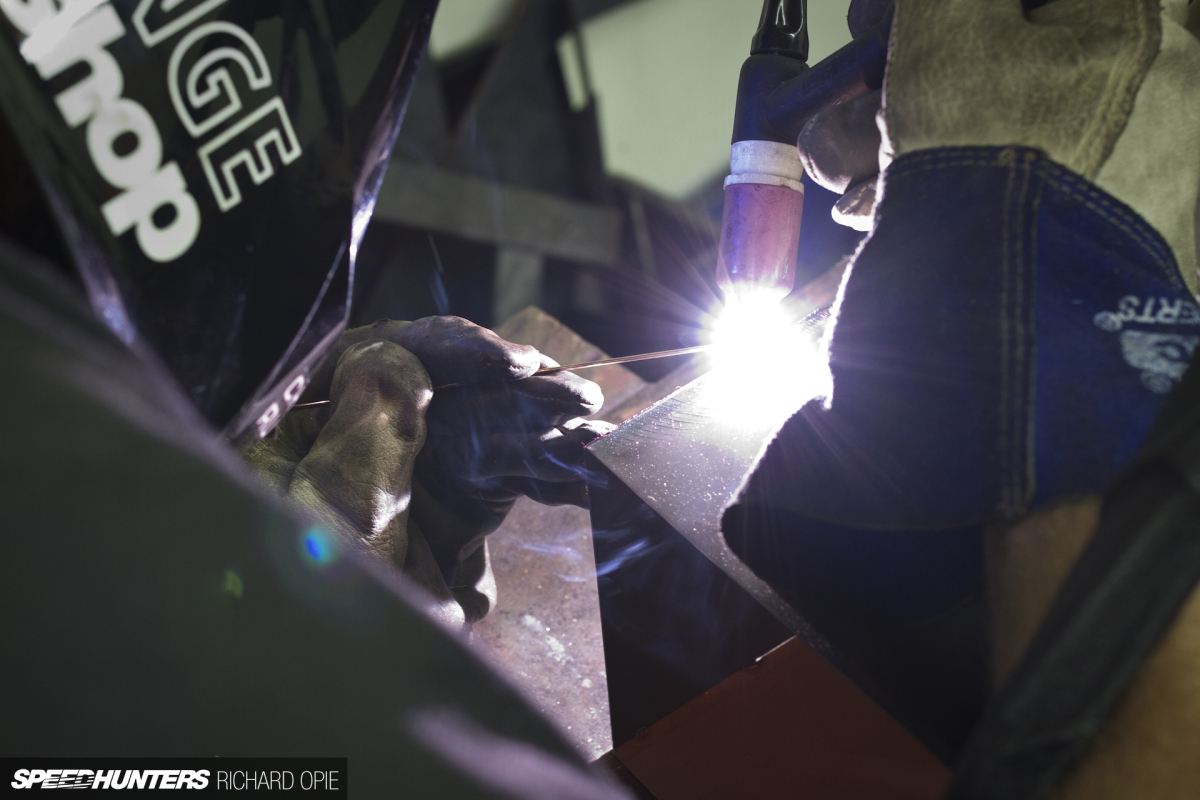
Step two was of course to TIG-weld the joins of the surge tank together.
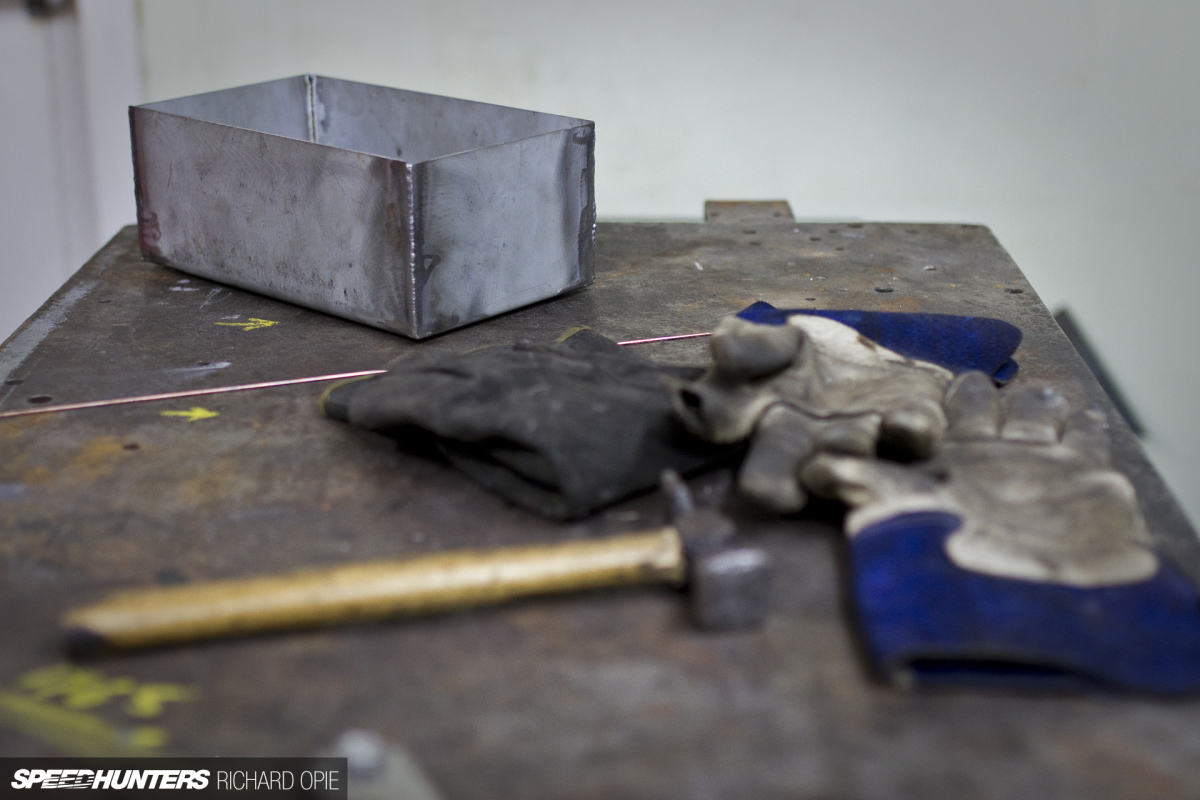
Then all of a sudden, a simple rectangular container is the net result, ready to be test fitted against the hacked up fuel tank.
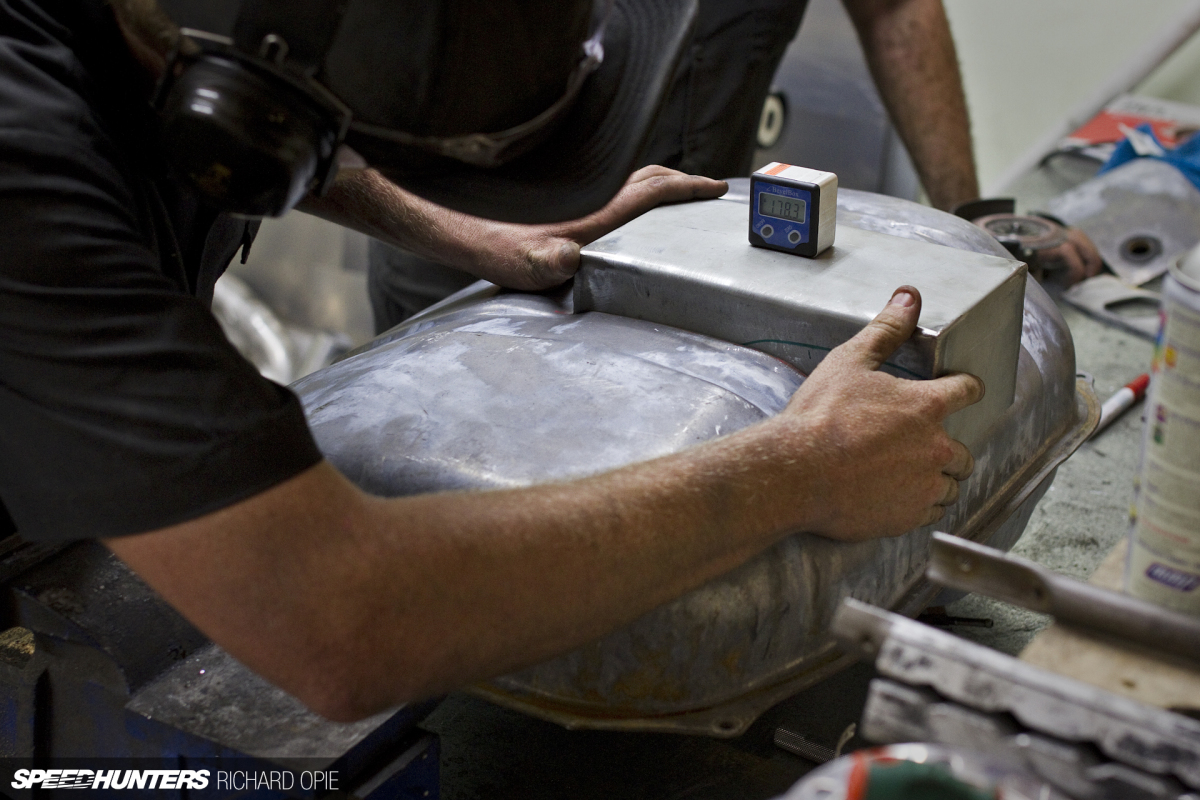
The initial test fit involved ensuring the surge tank was sharing the same vertical plane as the fuel tank would when mounted beneath the car. The seam running around the circumference of the tank offered a simple reference.
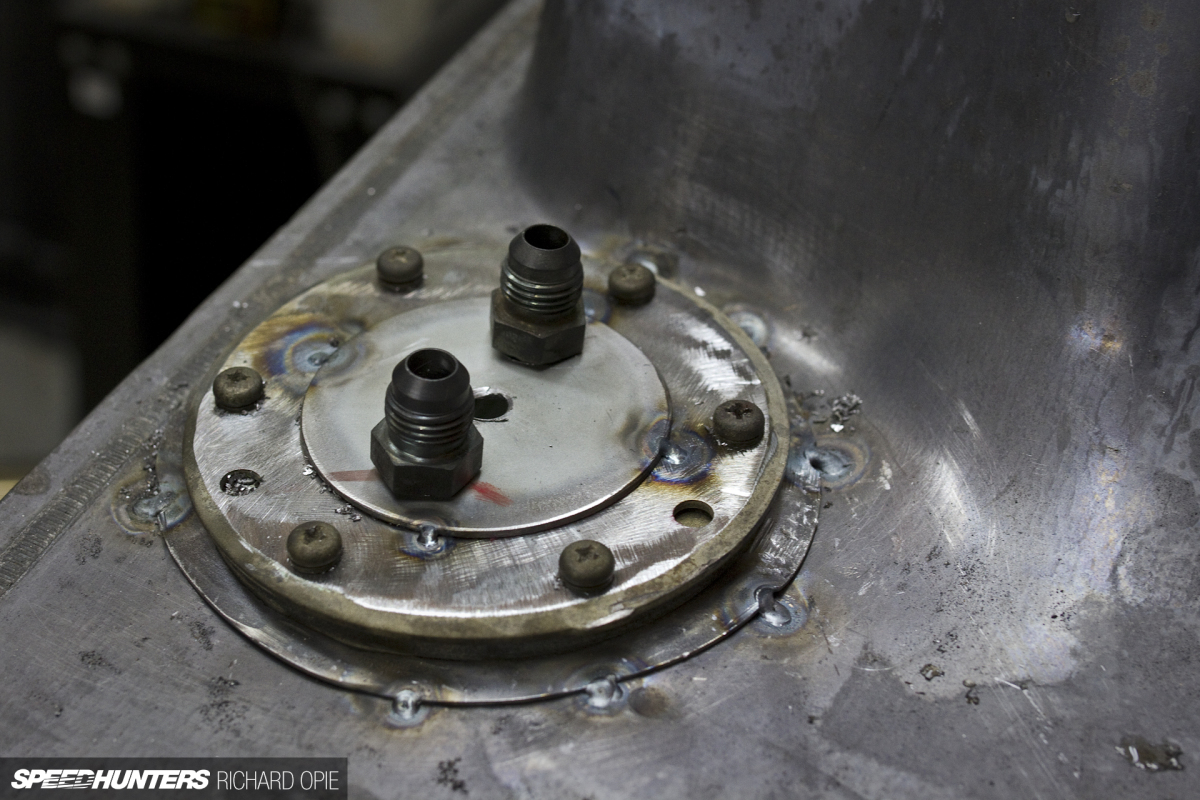
Tacked in, awaiting final welding the companion to the tank mounted flange began to take shape. Again born of a repurposed part, we elected to use a pair of -6AN fittings welded to steel feed and return lines below the tank with a steel cradle slung beneath accommodating the pump itself.
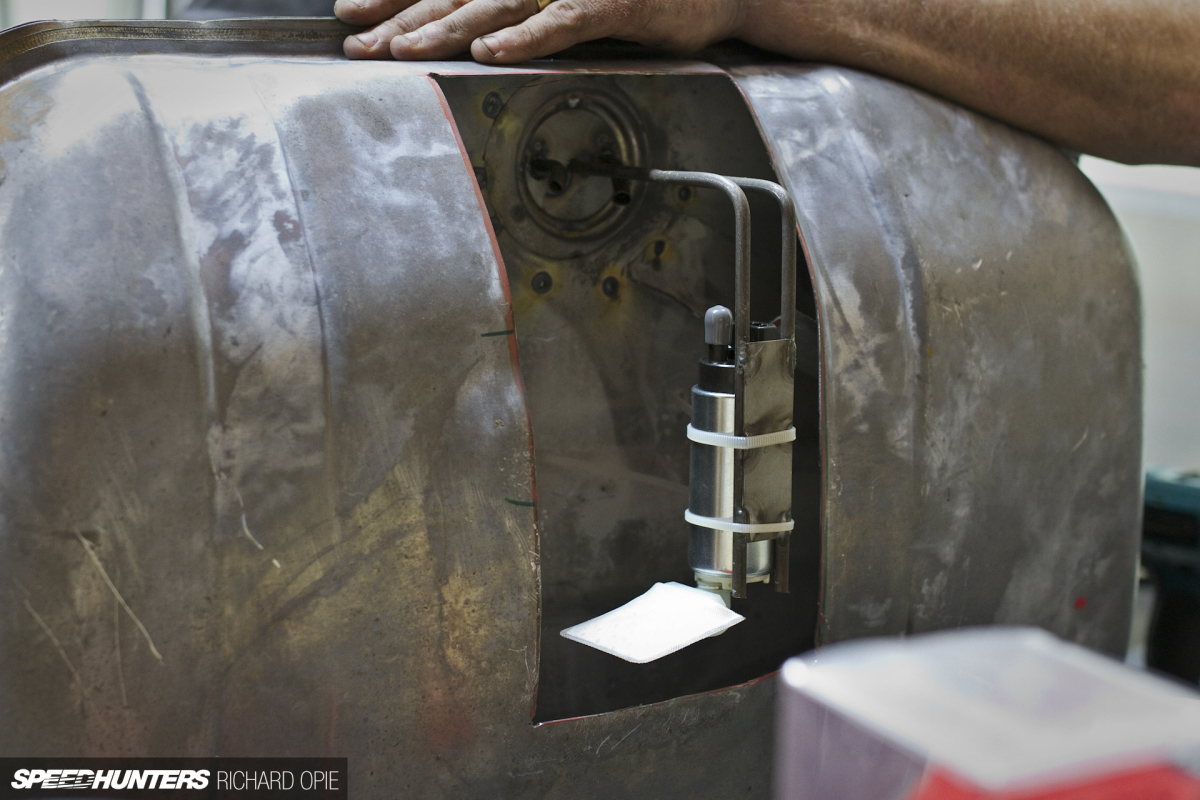
Without the surge tank installed, the assembly looks something like this – mounted on its side with ample fuel to draw from is a Walbro fuel pump with a flow capability exceeding that of the fuel requirements the 4A-GE might have.
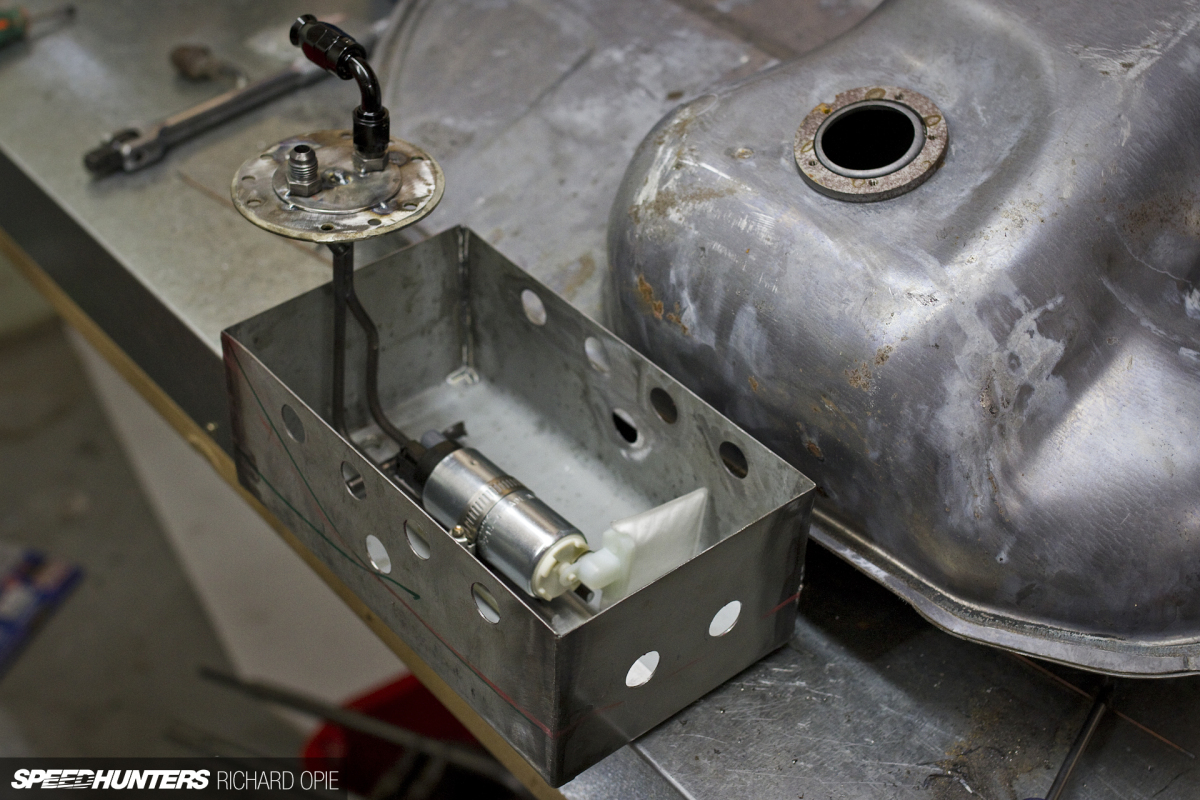
And out of the tank, the pump itself dummied up within the surge tank giving an indication of how the setup should work. As the walls of the surge tank protrude above the bottom level of the tank, several holes were required to permit the draining of fuel into this compartment, but sparing enough to trap fuel inside when levels get low to reduce possibility of fuel surge under cornering or acceleration. In theory, the fuel warning light will illuminate long before this is even getting near empty which I hope will provide enough of a safeguard to refuel.
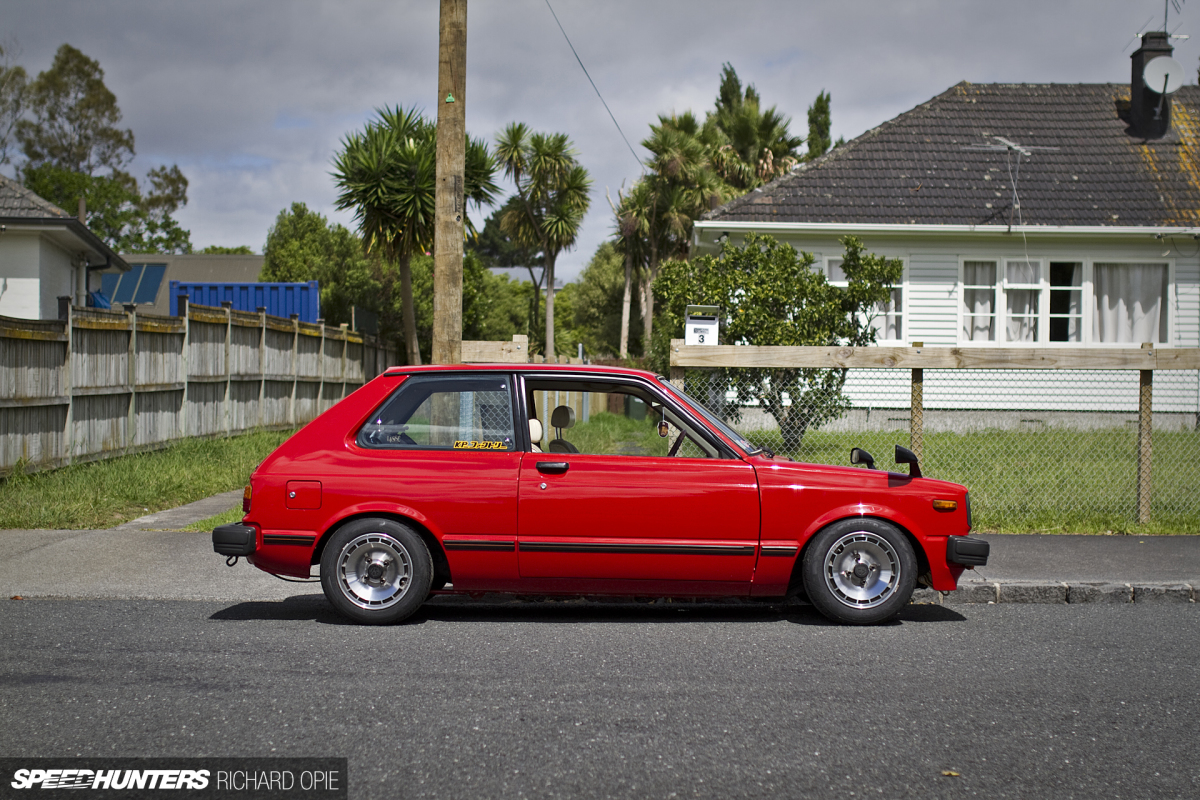
It’s a time-hungry process. So the next time the fab shop hands you an invoice, before disputing the cost definitely take a moment to consider the time and expertise spent solving the problem you’ve presented them. In my case the tank is not completely finished (awaiting final welding, leak testing and refinishing), but Project KP61 is definitely taking some giant leaps forward thanks to some talented fabrication assistance.
Next on the list is to bend up a variety of brake hard lines from the pedal box to each corner of the car, and then to start tackling the wiring loom and solve a couple of niggly little problems, one of which is finding a suitable heater tap to mount beneath the dash. Either way, I’m motivated, and blessed with some of the best friends a car nut could want to crack on with getting this thing to the finish line!
Richard Opie richy@speedhunters.com Instagram:
snoozinrichy