Thanks for the kind words.
Keep trying to tell myself, 'as long as it solid, and better than before you started, it's a pass'. So far so good.
The rear arch has me spooked a bit. I guess it's a fear if warping such a large panel.
I realised I have both front arch lips spare, which, when flipped left to right sides, match the contours and profiles of the rear arch.
Thats means I now have 2 arch sections, so I get a second chance if I mess it up!!!
So, with that, I've decided to trim down the front arch section and just do the bare minimum around the arch. Either lapped or but welded, not sure yet, however if it looks good, it'll stay.
If I'm not happy, I'll cut it out, and go with the larger rear guard section higher up the guard.
Here's how the front offside front guard fits the rear near side rear arch. The lower sections don't quite match however they are solid on the wagon and won't be needed.
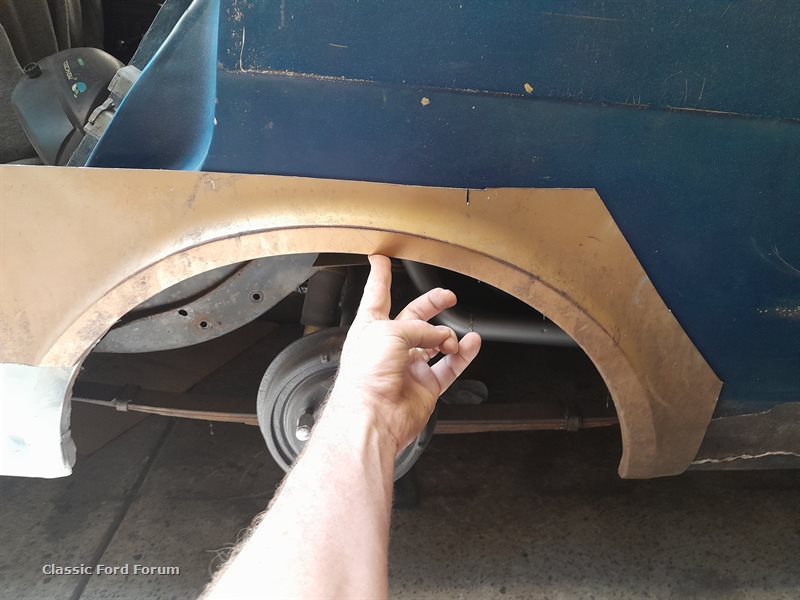
And here it is mostly trimmed to the flat section of the arch lip.
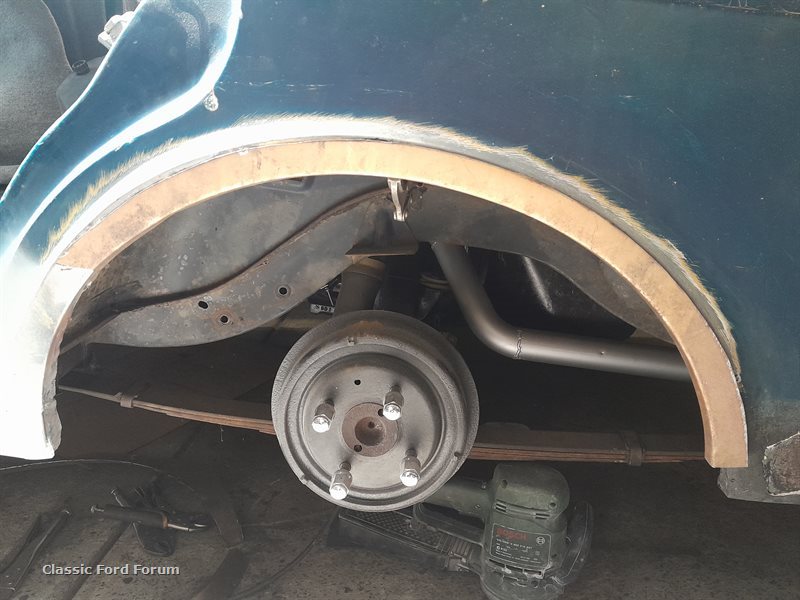
Will tackle it in a few days and let you know the results.
Attached Image(s)
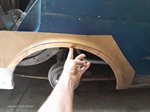
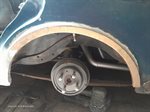