If it was my repair:
I'd probably want to focus on ideally being able to keep the top radious curve of the arch as the main key.
if you had a replacement section available in one of your cuts (or new), then I'd take the cut back to about 1" high near the door corner and straight across (red line). Mind you, any old cut section you might have though is possibly in the same condition.
Second option would be along Martys suggestion, the Green line repair. Make a block of timber with the same radious as a rough die, and hammer down a fold thats 10mm thick or so to become the inner guard lip. You might have to tackle it in 3 or 4 sections, repairing a few inches long each time.
Without a shrinker to pull in the curve it might be a bit harder.
I have a shrinker same as Martys, but still have done all bits manually.
That top bit of the curve is going to be thin, from the rust and also the original stamping.
If it looks like its too bad to weld, you might have to make each repair section taller, to include the top arch curve return also.
You could even fold the top return back a little shorter, tucking it under whats there, and plug welding through the original panel into the new patch. Hope that makes sense.
Then the 'exposed cut edge' of the original could be seam tacked off where you can to finish off.
This would give you as much new metal to work with, and you are mostly welding onto the new infilled bits wherever possible rather than butting to really thin steel.
Good luck. In the end, you just need something solid, and a skim of filler will help to shape out and curves that arent right.
Attached Image(s)
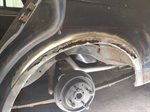