2012So this is what I did during 2012
I finished the engine mountings, now to the gearbox mountings
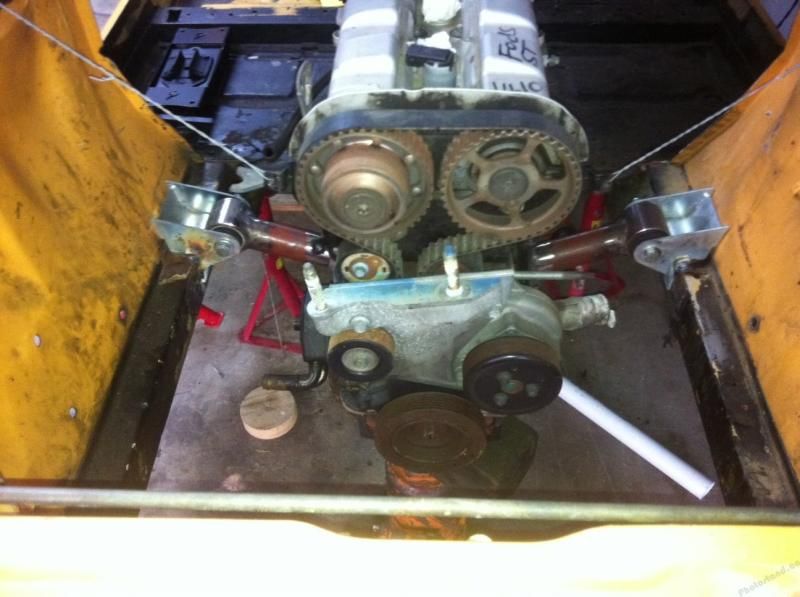
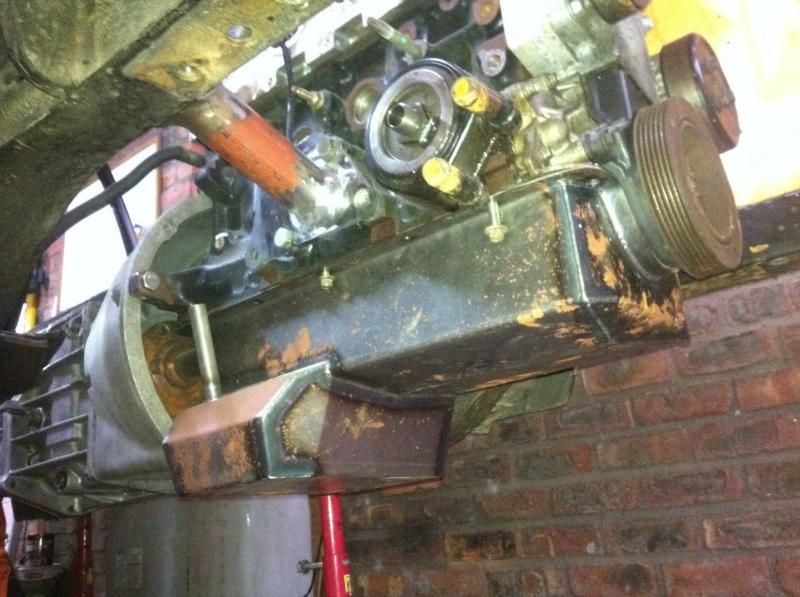
I have moved to the back end of the car as I am waiting for somebody to bring me my gearbox mounting steel.
I had to put the wheel arches back on to establish the center line off the rear axle.
I have cut the slots for the 4 link system. Removed the rear seat mounting and where busy removing some more unwanted steel.
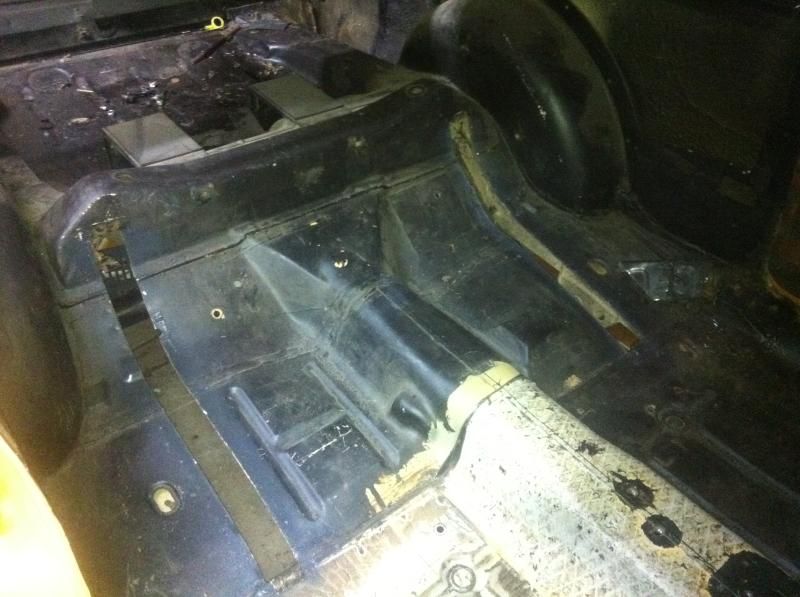
In between my build I bought and fixed up a Mini to do some Gymkhana, the urge was there to be involved in some racing.
This actually took allot of my time as it broke as much as I raced it.
It went from supposed to be a cheap no maintenance interim gymkhana replacement car to costing me allot off unnecessary bucks and taking up all my free time.
See problem below
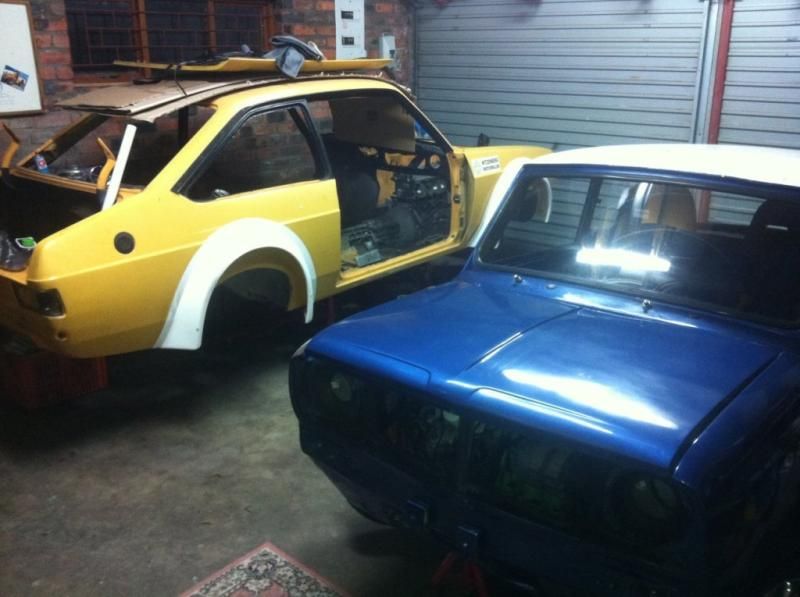
Ok, back to work on the FORD,
I have picked up a sponsor for the Mini so now I have someone to help out on the Mini, thanks Mini Service Centre
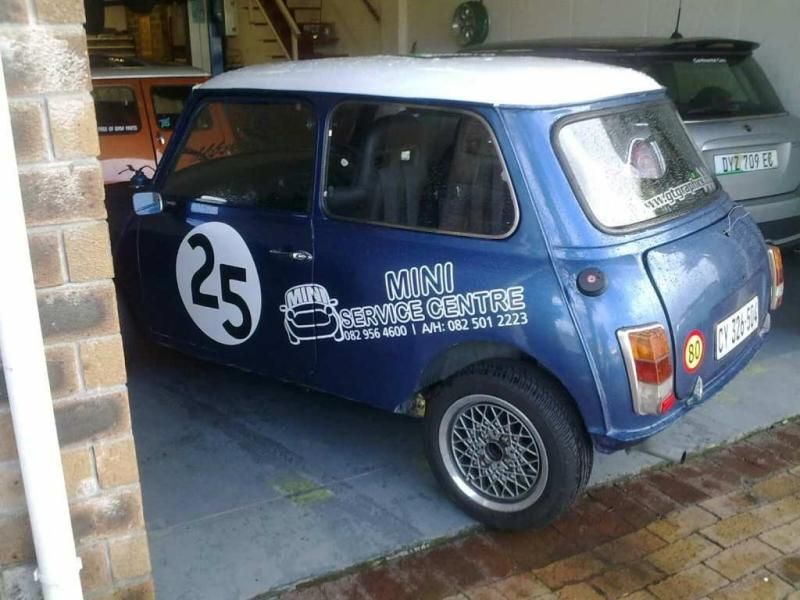
I now had more free time for my Scort
I have cleaned out the inside of the body of all the unnecessary metals and double plates in preparation for welding in the new parts.
I sent my gearbox mounting drawing in for laser cutting and bending, got that back.
The reason for the long strait bottom is so that I can run the exhaust between the gearbox and in the tunnel.
I did not want to go below the mounting for the exhaust because then it would be too low as I have already mounted the engine and gearbox as low as possible.
Also did not want to make an additional tunnel next to the bracket just for the exhaust.
I made some top plates for extra support which I will most probably weld in.
Once I cut back the tunnel there will be enough space for the exhaust.
Since the last update I completed removing all the double plates. Really f up my back on this, still in pain
Next up is to clean the metal for welding. I will then start welding in the 4 link boxes soon
Started making my new gearbox tunnel out of wire and cart board as a sample before I get to the metal work
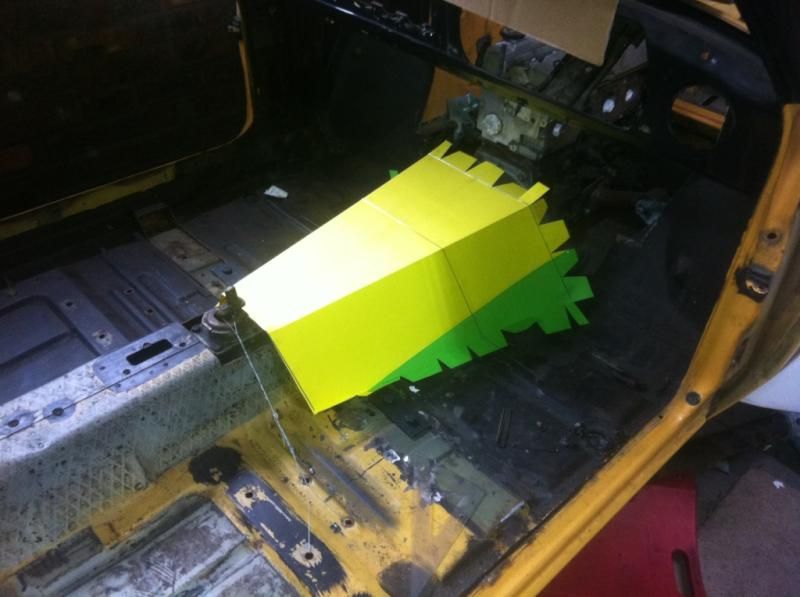
For some this might not be a big deal, even only a second nature.
After some practice and even giving up I eventually got the hang of TIG welding
Did some practice
Started with the 4 link kit. Did some spot welds to keep it in place.
Think the welding so far looks good
I am now confidant to weld the car and must say proud that I have the hang of TIG welding
Have been working on the welding of the 4 link brackets. I find the most difficult part of the welding the uncomfortable positions that I have to weld in. It is a slow process as I can only weld in a certain position for about 15 minutes.
This is what is welded so far
While I take breaks from the welding I started working on closing the front fire wall. I use the tig welding rods and bend them in the shape that I require. From there I will make a cart board sample and then move on to the plate. I am planning on buying some 1,2mm electro galvanized plates to start closing all the big holes in my Ford
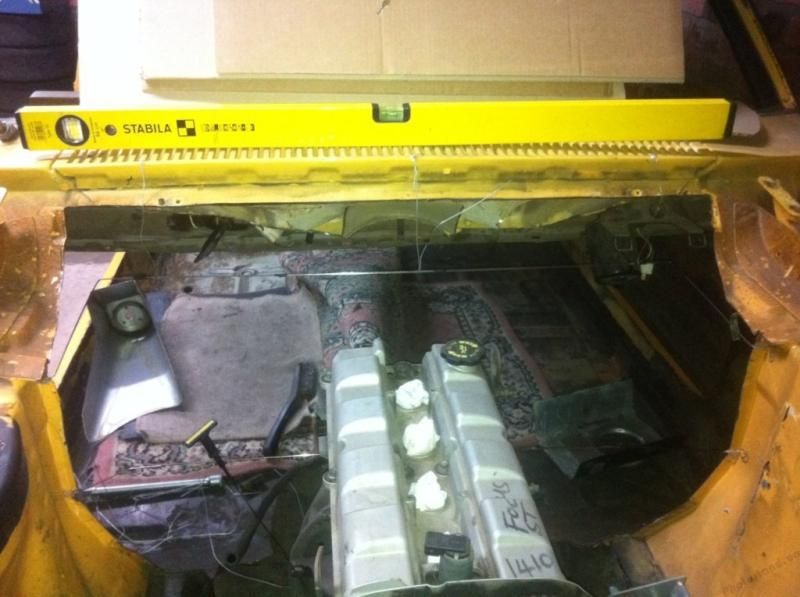
Have anybody fitted the turrets as supplied from Rally design or from other suppliers or your own. Mine does not seem to puzzle in???.
Last one. Is the best way to mount your rear coil overs on your axle 100% vertical, angled or what is the theory behind this?
I picked up my sheets of 1.2mm electro galvanized sheets.
I then started with the gearbox tunnel.
I have decided to bend the sheets myself.
How I did this was by clamping down two pieces of steel on top of the sheet on the work bench on the line of where I wanted to bend the steel. I did put a piece of 1.2mm metal sheet in the middle under the plate as I found that the forces in the middle of the steel used for clamping was bending slightly and this resulted that the middle of the sheet making a long bend and not as sharp as at the ends. I pushed the plate evenly to get my desired angle.
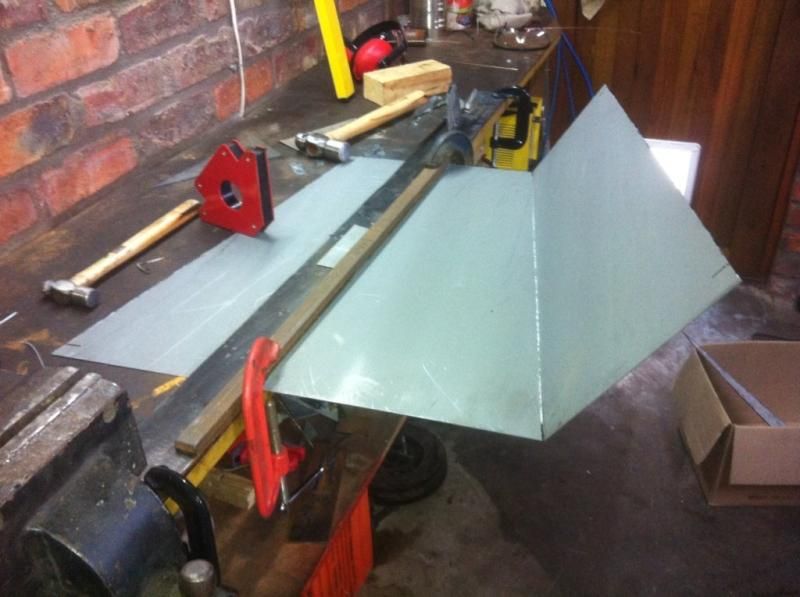
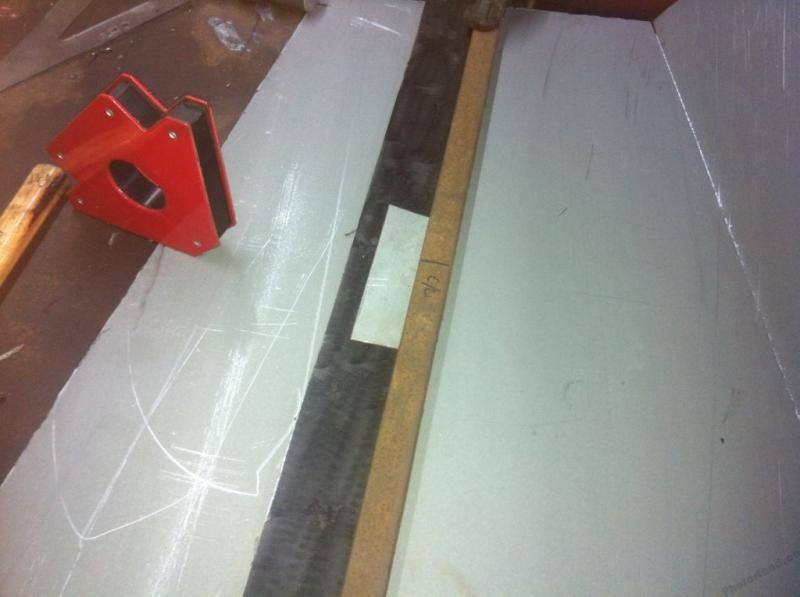
I used a block of timber and a hammer to get a slightly sharper bend. I use the timber block to spread the blow of the hammer to prevent dents. I still got some dents but you can hardly see them. Can more feel them
The result - my gearbox tunnel
I have cut the last bits of steel out for the new tunnel.
There is now more than enough space to run the exhaust next to the gearbox
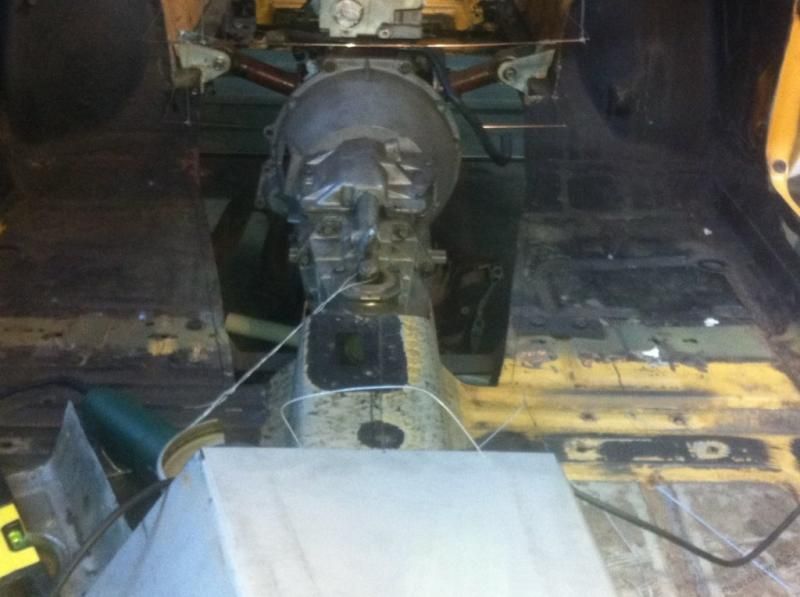
Now just to weld in
Gearbox tunnel welded in
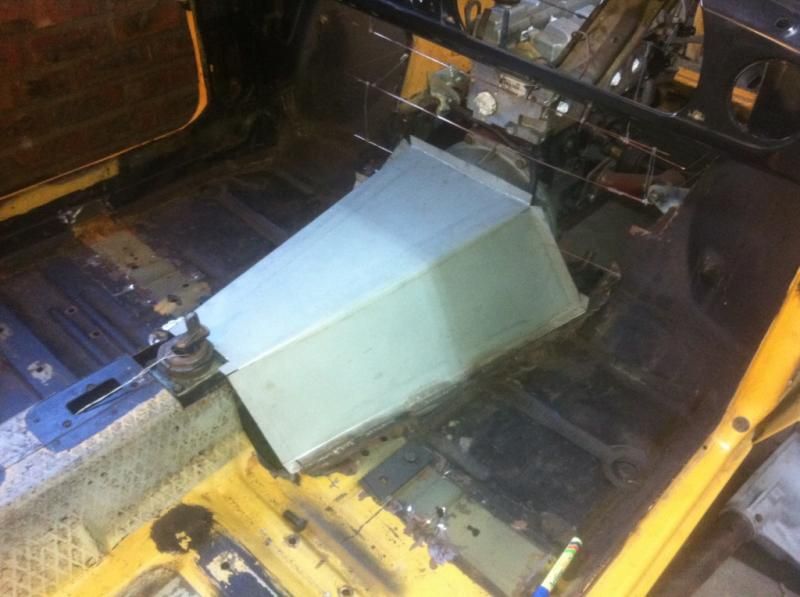