OK, a few hours today and the sections are welded in and 90% completed. I have not ground down all the welds completely as time was running short so I threw some primer on it to keep it from rusting etc.
The weld through primer mentioned in the thread below was used on all mating surfaces and seemed to work a treat - not burning off etc.
http://classic-ford.org/forum/topic.asp?TOPIC_ID=16632
First section tacked in
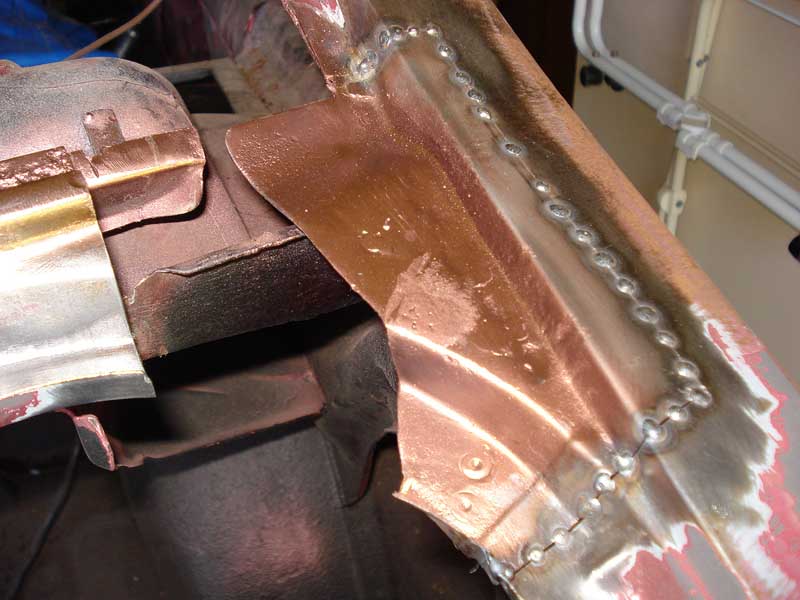
Majority of the welds knocked off from the first section and found a few pin holes which required a second go. Final section welded into place.
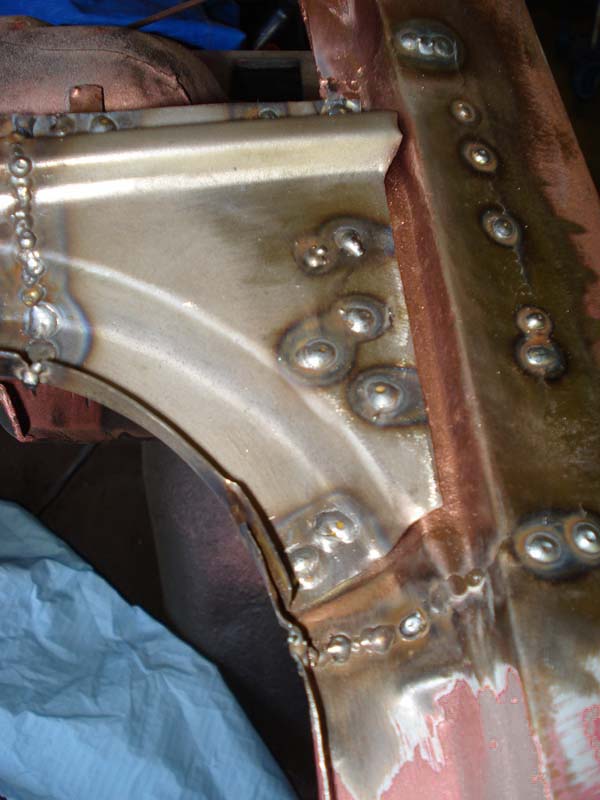
Majority of the welding ground back and a lick of primer. A little skim of filler should have this looking fine
