I've had this in the box for nearly a year, kind of bought it near the end of winter , as we're heading into the cooler weather I took the heater into the shed and thought ways of installing it without being in the way. This is an 8kw diesel heater which is 12v
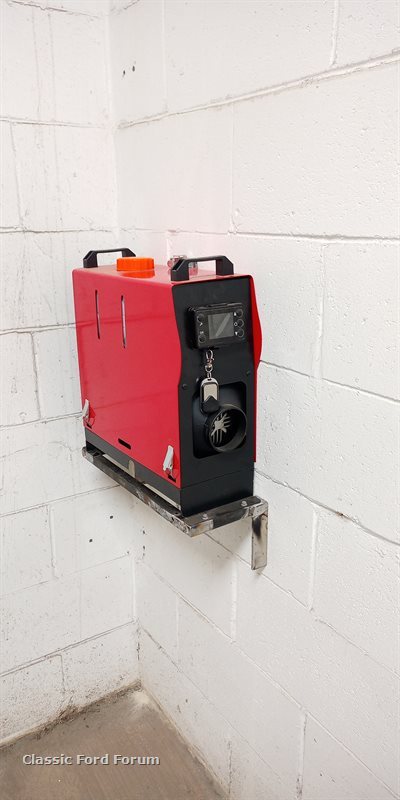
More to make Deano smile is I used gasless dry weld the mounting shelf and screwed to the brick wall. As the heater comes with tubes and exhaust pipe to help install in the truck or caravan etc, but I
went a bit further. I found a length of poly pipe and used that for the cold air intake , I used plastic plumbing elbows and heated the tube to allow them to fit tight.
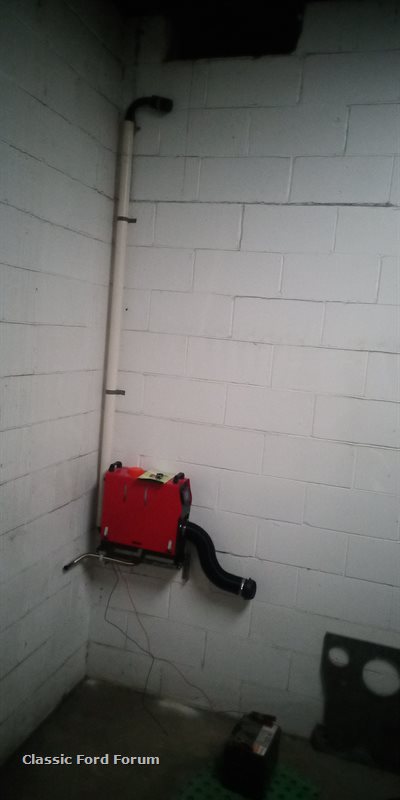
Next was to find something for the exhaust pipe, I found a derelict metal ladder in the steel pile and thought, that'll do perfectly, I just needed to shrink the joiner down to 25mm so the flex pipe slides into, I just V slotted the end and hammered them together and welded. I make mounting tabs to screw into the wall with. Then it needed to go up the wall so a intermediate piece was cut and welded on then the vertical piece welded on.
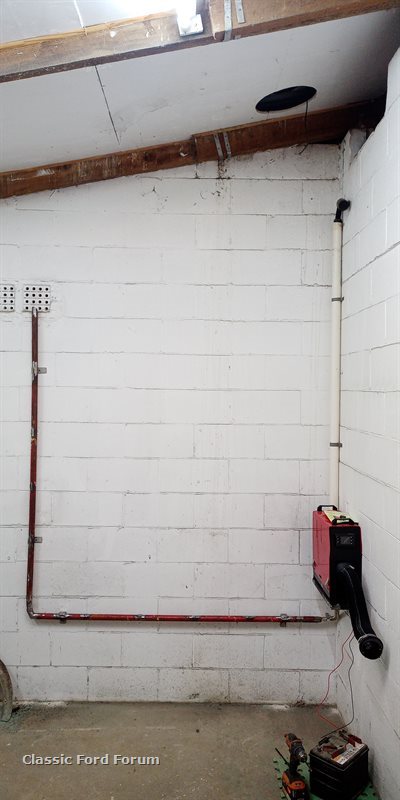
And this is the end bit aiming to the brick vent holes
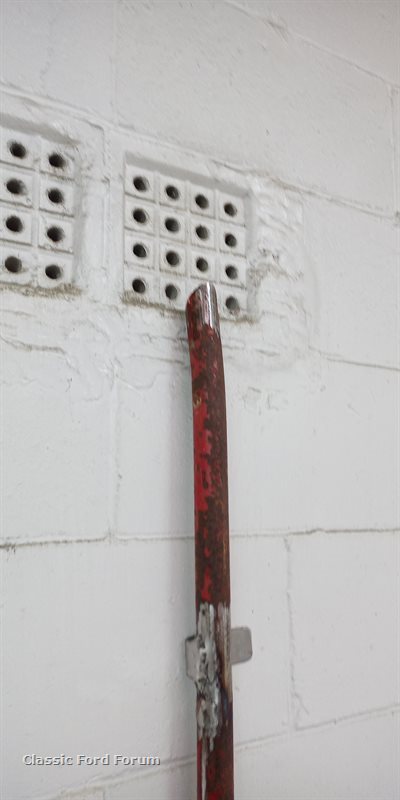
Today I made an enclosure for the exhaust so it can only go out the vent, it was made from thin gauge sheet and folded to shape. There is also high density foam around the edges and the pipe intake hole. Once the heater gets to temp I went outside to check on the exhaust, it's very minimal and hardly any fumes, I suppose when they use about 200mls an hr on low setting it's pretty good
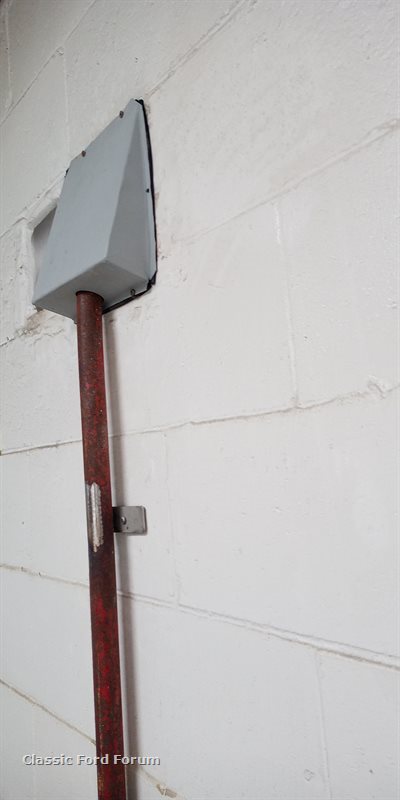
Now I can take on winter without going cold !