Moving into the rear gutter channel which was about 650mm long , from the back of the door shut right to the end at the back.
For anyone needing a piece of gutter to make, watch these pics.
First off is choose your metal, I decided to go a bit thinner (0.9mm) as there's plenty of right bends involved. The first fold is the outer top gutter which folds back inside flat, this was the hardest to do as only about 3mm or so overlap is ample, once it's folded it needs hammering over flat .
Next is to accurately scribe the next fold line, stuff this bit up and it's start it all again, check and check again as this bit is the outer gutter which is seen by everybody.
Once the strip is folded and should be just over 90deg, this part is where things get fun, lightly working on the shrinker to get the curve to line up with the cars roof, and then stretcher lightly on the outer channel to get the curve down to match the swing of the body. Once happy it's over to the bead roller with the stepping wheels to create the hard to copy drop curve below the outer edge, I ran the piece through 3 times but needed to re stretch and shrink the piece to fine tune it .
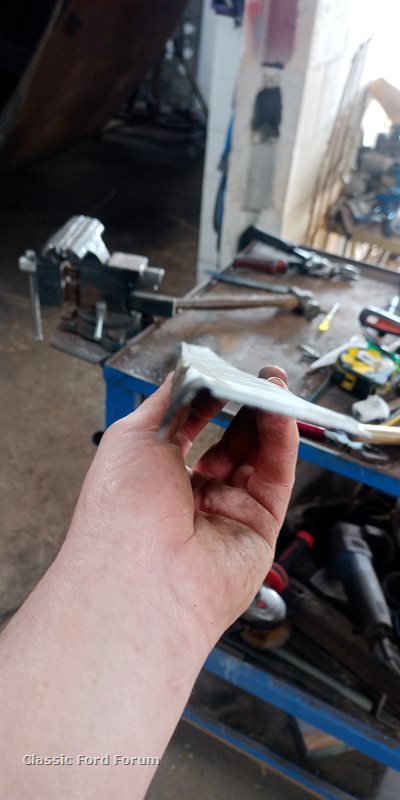
This is that drop curve to replicate original
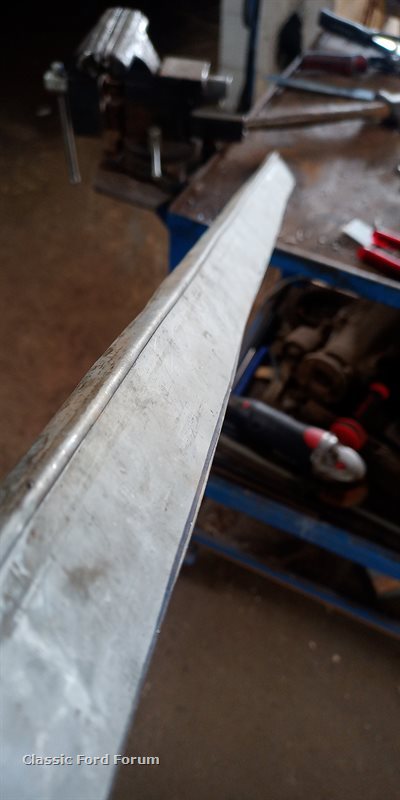
The double curve, back and down
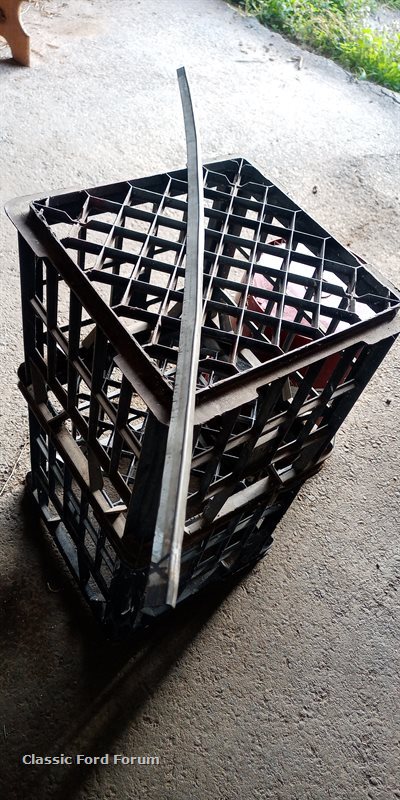
This is the part offered up to the car, car is upside down to make work easier
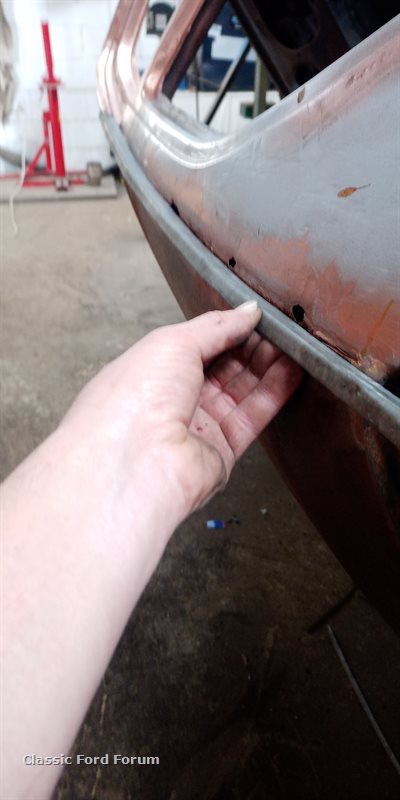
Those 3 rust holes got plugged up before any other welding as it's easy to tackle now than later.
Before I could fit the gutter, I decided to weld a strip to the roof channel, this was also shrink stretched to fit, I welded it to the quarter panel and then to the roof panel to stop any floppy loosened, welded were tacks every 1/4 inch which is plenty, they were shaved back flat so the gutter channel would sit flat against it
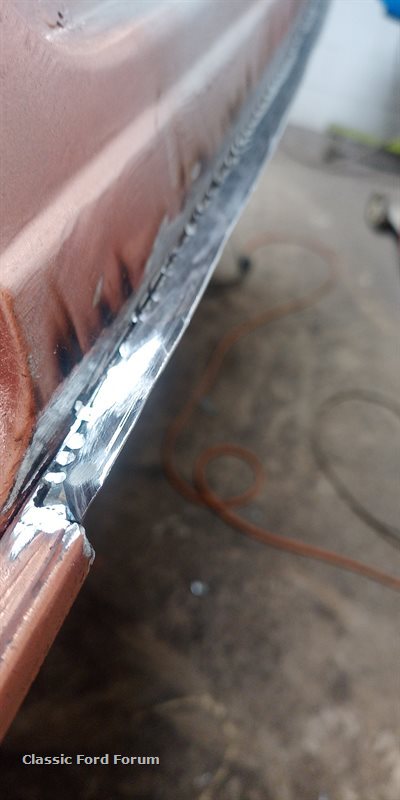
There was some extra welding as needed and sanding for a nice finish.