buoyed by my apparent improvements in welding skill, i decided to have another crack at the drivers side window panelling.
These were one of the first jobs I'd had a crack at while learning, and on this side I kept blowing through. In the end, I got so disheartened by it no matter how I tried, I needed to cover it over with cardboard for a few months to avoid seeing the failures.
So take 2:
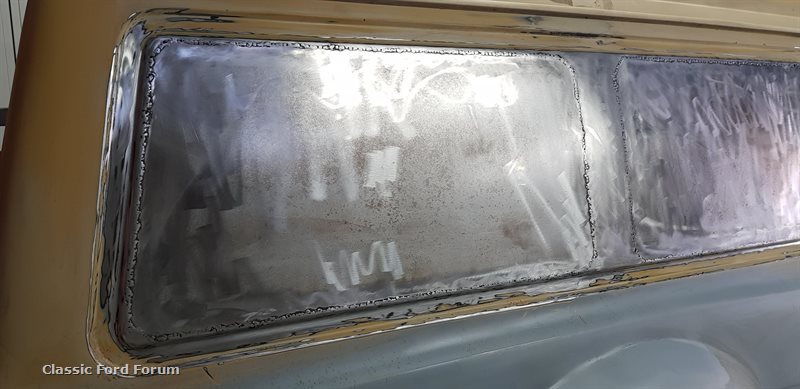
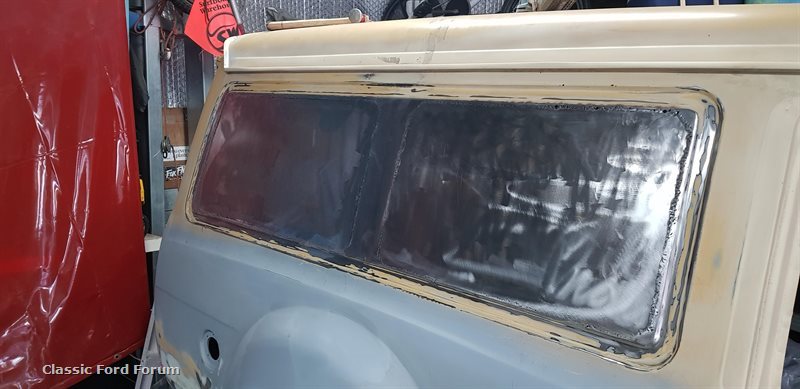
In the end, it wasn't the welder settings, it was all down to technique. I think it was Blue that suggested how close I was holding the gun, and also the angle. This and practice, practice meant that now about 90% of the time I could redo a blowthough and add material, rather than blow it out worse. Still not a welder, but it was a good rainy day in the garage.
Again some filler, and a good sand should see a nice curve hopefully.
Oh yeah, I almost set fire to the garage too. I usually wax and grease remove right before welding. I did this on the roof vent delete, but absentmindedly left the chux cloth right next to the patch. Grabbed the torch, lets god. First dab with the gun and woof! total flames from the chux, about 1/2 foot high. I was on a ladder, going ****, ****. The nearby extinguisher was on the bench, so I jumped down and grabbed it. By this stage, the chux still looked impressive, but if I shot it with the extinguisher, it was sure to blow off the room and set something else alight.
I know, bat it out with your glove idiot. Yes ok, . Left welding glove did a bit, but flames still too large. Use both hands.
Unfortunately rh gove was a mechanics glove. It did it, but the palm melted. Still the fire was out, just a bit of ouch peeling of the melted glove... Another one not to tell the boss about. What happens in the garage as they say.